认 证:工商信息已核实
访问量:1118535
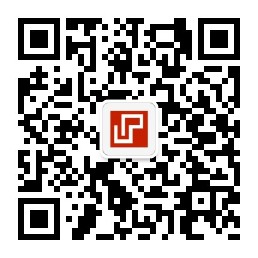
青岛联瑞精密机械有限公司 2017-11-30 点击2777次
I. INTRODUCTION AND PRINCIPLES
In this presentation we will discuss the principle of the Attritor and its applications. The Attritoris a grinding mill containing internally agitated media. It has been generically referred to as a“stirred ball mill.” There are quite a few types of Attritors; we can categorize them as dry grind
Attritors, wet grind Attritors, regular speed Attritors, and high speed Attritors.
A useful and simple equation describing the grinding momentum is M x V (mass x velocity),
which enables us to see how the Attritor fits into the family of mills. For example, ball mills use
large media, normally 1/2” or larger, and run at a low (10-50) rpm. The other mills, such as
sand, bead, and horizontal, use smaller media from 0.3mm to 2mm, but run at a very high rpm
(roughly 800-1200). High speed dispersers with no media run even faster rpm (1200-1800).
Various types of Attritors fall in between these. (See chart, Comparison of Grinding Mills,
below).
COMPARISON OF GRINDING MILLS
TYPE OF MILL MEDIA SIZE RPM TIP SPEED
(fpm)
Ball Mill 1/2” and larger 10-50
Attritor 1/8” to 3/8” 75-450 600-1000
Sand Mill/Horizontal mill 1/64” to 1/8” 800-1200 2000-3000
HSA Attritor 1mm - 3mm 400-1800 2600-2700
HQ Attritor 0.4mm - 3mm 1000-1900 3000
High speed disperser ------ 1200-1800 5000-6000
The most important concept in the Attritor is that the power input is used directly for agitating
the media to achieve grinding and is
not used for rotating or vibrating a
large, heavy tank in addition to the
media.
For efficient fine grinding, both impact action and shearing force must be present, Fig. 1. When wet grinding in the Attritor, impact
action is created by the constant impinging of the grinding media due to its irregular movement. Shearing action is present in the Attritor as the balls (media) in their random movement are spinning in different rotation and, therefore, exerting shearing forces on the adjacent slurry. As a result, both liquid shearing force and media impact force are present. Such combined shearing and impact results in size
2
reduction as well as good dispersion.
The principle of Attritor dry grind processing is achieved by an expanded moving bed of media.
This condition is described as kinematic porosity. The dry particles are subjected to various
forces such as impact, rotational, tumbling, and shear; therefore, micron range fine powders can
be easily achieved. Additionally, combinations of these forces creates a more spherical particle
than other impact-type milling equipment.
The Attritor’s versatility is gained by the ability to operate under a broad range of conditions.
For example, grinding media type, size, and amount; different machine speeds; variable loading
or feed rate of raw material. In addition to reducing particle size, Attritors also can create the
highest intensity intimate blending of dissimilar materials. Specific chemicals or additives can
also be introduced to the mill during the grinding process to achieve the ultimate dispersing or
coating on the dry solid particles.
II. GENERAL FEATURES AND OPTIONS
• Various types of Attritors can be used in wet or dry grinding process.
• A series of metal-contamination-free machines are specially designed for the ceramic
industry. Several types of ceramic and polymer materials have been developed to line or
sleeve the machine’s internal parts. These materials include alumina, zirconia, silicon
carbide, silicon nitride, tungsten carbide, rubber, polyurethane, and various plastics.
• Laboratory size Attritors are designed with variable speed drive for different RPM selections.
Grinding tank sizes from 100ml to 9.5 liter.
• Production size Attritors are equipped with a specially designed 450% high torque motor for
easy startup. The motor has two speeds - high speed for actual grinding, and low speed (1/3
of the high speed) for charging, discharging and cleaning procedure. The machine capacity
ranges from 35 liter to 3800 liter.
• All grinding tanks are jacketed for cooling or heating.
• A torque meter can be equipped to measure the energy input, and by using the total power
consumption, one can monitor the grinding process.
• Cover seals can be provided for processing under inert atmosphere.
III. THREE BASIC TYPES OF WET GRIND ATTRITORS Fig.2
BATCH ATTRITORS (“S” MACHINES) The operation of the batch Attritor (Fig. 2) is very simple. All the material can be loaded
directly into the grinding tank; no premixing or pre-dispersing is needed. Since the top-open grinding tank is stationary, the process can be visually observed and corrections and additional ingredients can be introduced at any time. The maximum feed material size can be up to 10mm, provided the material is friable; otherwise, any 10 mesh down material is feasible to be processed in this machine.All production “S” machines are equipped with
3
a built-in pumping system which maintains circulation during grinding for accelerated attrition
and uniformity. The pump can also be used for discharging.
Batch Attritors are used to process hard-to-grind materials, such as tungsten carbide, silicon
carbide, and various metals. High viscosity slurry with up to 30,000 cps can also be processed
easily in batch Attritors.
CIRCULATION ATTRITOR (“Q” MACHINES) (Fig. 3)
This system is a combination of an Attritor and a holding tank which is generally 10 times the
size of the Attritor. One of the essential requirements of the Q-Attritor system is the high
circulation (or pumping) rate. The entire contents of the holding tank are passed through the
Attritor at least once every 7-8 minutes.
At this rapid speed, the premixed slurry is pumped through a confined media bed. The media act
as a dynamic sieve, allowing the fines to pass through quickly, while the coarser particles follow
a more tortuous path and are ground finer. (Fig. 4) The slurry can be continuously monitored,
additional ingredients can be added to the premix tank at any time during the grinding, and the
processing can be terminated precisely.
Fig. 3Fig.4
One advantage of the circulation system is that large quantities of material can be handled with a
smaller investment of grinding media and Attritor equipment. Another advantage of the “Q”
Attritor is better temperature control, which is achievable for two reasons:
1. The holding tank is jacketed for cooling or heating and acts as a heat sink.
2. The slurry passes through the grinding chamber very quickly (20-30 seconds per pass),
therefore having less time to heat up.
These advantages are very important when the grinding chamber is lined with plastic or rubber
for metal-contamination-free processing.
CONTINUOUS ATTRITOR (“C” OR “H” MACHINES) (Fig.5)
4
C-machines are best suited for the continuous production of large quantities of material. H-machines are built the same as C-machines, but use smaller media (2-3mm) and run 60-70% higher rpm.
A well-premixed slurry is needed to be able to use this type of process.The slurry is pumped up through the bottom of the tall, narrow grinding tank and discharged out the top of the tank. The residence time required for certain fineness is controlled by the pumping rate.The continuous Attritor can be set up in a series, using larger media and grid openings for the coarser feed, then the subsequent units with smaller media to achieve the finer grind.
IV. ATTRITOR GRINDING MEDIA TYPES:
Selection of grinding media depends upon several factors, some of which are interrelated.
• Specific gravity. In general, high density media give better results. The media should be
more dense than the material to be ground. Also, highly viscous materials require media
with higher density to prevent floating.
• Initial feed size. Smaller media cannot easily break up large particles.
• Final particle size. Smaller media are more efficient when ultrafine particles are desired.
• Hardness. The harder the media the lesser the contamination and consequently, the longer
the wear.
• pH. Some strong acid or basic material may react with certain metallic media.
• Discoloration. For instance, white material should remain white.
• Contamination. The material resulting from the wear of the media does not affect the
product or can be removed by a magnetic separator, chemically, or in a sintering process.
• Cost. Media that my be 2-3 times more expensive may wear better, sometimes 5-6 times
longer, therefore, well worth the extra cost in the long run.
Following is a list of types of grinding media used in the Attritor:
through-hardened carbon steel aluminum oxide
chrome steel steatite
440C stainless steel tungsten carbide
zirconium silicate silicon nitride
zirconium oxide (MgO or Y2O3 stabilized) silicon carbide
V. NEW DEVELOPMENTS“SDG” AND “HSA” DRY GRINDING ATTRITORS WHY ATTRITOR DRY MILLING?
• Process Economics: Attritors are energy efficient, compact, easy to operate, and require
low maintenance.
• Versatility: Attritor’s design allows modification of numerous variables to adjust changing
specifications and meet the final product requirements.
5
• Reduced Transportation Costs: In many wet slurry processes, 50% of the gross weight is
liquid.
• Energy Saving: Removal of the liquid from a wet grinding process involves not only
another process step, but also requires large amounts of energy.
• Eliminate Waste Liquid Disposal: Following stricter environmental regulations, the
disposal of any waste liquid (water or solvent) is very costly.
The SDG Attritors use grinding balls from 5mm to 13mm. The shaft RPM generally runs from
75 to 500. This series of Attritors are suitable for harder-to-grind materials such as metal
powder, metal carbides, and glass chunks. The feed material size for these machines can be
quite coarse, but smaller than the grinding media chosen.
The SDG Attritor is also used to make dispersion strengthened metal (DSM). In this process
(known as mechanical alloying or cold welding), the kinematic porosity results in grinding
media breaking the metals and additives into small particles first, then beating them together to
form agglomerates. By repeating the process, the various metals are evenly mixed and dispersed
to form a new composition of alloy (DSM).
Pigment industries also use SDG Attritors to dry grind some pigments for their color
development.
HSA (High Speed Attritor) was newly developed in the past few years. These machines feature
a unique patented design concept that includes a new grinding tank internal configuration and
side discharge screen which allows mills to run at higher speed, using smaller media, and
continuously discharges products out of the mill by centrifugal force. (Fig. 6)
HSA Attritors generally operate from 400-1800 RPM using grinding beads from 1-3mm. This
combination of high velocity and increased grinding media surface area insure much finer grind
of the processed material.
The HSA Attritor is generally used in a continuous mode. The material is charged into the mill
at the top by a pre-set rate feeder, and discharged out the lower side of the grinding tank. HSA
Series Attritors are generally used for finer feed material (-40 mesh), and produce large
quantities of ultra fine powders in micron size. Applications include various minerals such as
calcium carbonate, talc, barium sulfate, iron oxide; and rice hull ash and flyash. The HSA is also
often used for fibrous and polymer types of materials.
An air classifier or screen can be incorporated with SDG or HSA Attritors to form a closed
grinding process loop. By constantly taking out the fine product and reloading the oversize
particles, one can achieve very efficient narrow distribution fine grinding. (Fig. 7)
COMMON APPLICATIONS FOR DRY GRIND ATTRITORS:
Ceramic Powders Ferrite Fibers & Cellulose
Glass Frits Pigments Food Products
Metal Powders Minerals Plastics & Rubber
Mechanical Alloying Coal & Coke Chemicals
Metal Oxides Graphite
DISCREET PASS SMALL MEDIA MILL (DELTAMILL)
DMQ ATTRITOR
The DMQ is the newest member of the small media mill family. It is a hybrid of the
Deltamill and the QC mills. Like the Deltamill, it utilizes Delta discs. This
proprietary design eliminates shaft whip and mill vibration, while providing much greater
random media motion for improved milling efficiency. The mill is designed to accommodate media from 0.3mm to 1.0mm.
As with the Deltamill, the discs are indexed to provide directed and uniform media distribution throughout the mill chamber. The
mill can be used in both continuous and circulation modes. All of the mills can be produced with metal-free components for
certain ceramic applications where that may be a consideration.
The mill incorporates the separator design like that used in the QC mill. It consists of a series of rings with the appropriately sized spacer between them and is thicker than the older wedge wire screen. This new design virtually eliminates plugging of the screen.
Thanks to this rugged and large open screen area positioned at the end of the mill, servicing and cleaning are much easier than with other mills. It’s a simple matter to pull the cover off the end of the mill, which readily exposes the separator for servicing.
ADVANTAGES OF THE DMQ MILL
1. Operates in circulation or continuous mode
2. Uses media from 1 mm to 0.3 mm
3. Delta discs eliminate shaft whip and mill vibration
4. Delta discs provide greater random media motion
5. Indexed discs provide uniform media distribution
6. Service is fast and easy
7. More durable screening mechanism
8. Milling efficiency is improved
The graph shows the increased efficiency of the DMQ mill vs. the Deltamill grinding calcined clay
with a starting size of 3.6 to 3.7µ.
VI. SUMMARY
I. ADVANTAGES
1. Fast, efficient and reliable fine grinding
2. Versatility of the process
3. Low power consumption
4. Machine tank jacketed for cooling or heating temperature control
5. Easy and safe to operate
6. Low maintenance
7. Compact design, small plant area required
II. LIMITATIONS
1. Feed material size is limited to less than 13mm for SDG Attritors.
2. For most of the sub-micron superfine powders, wet grinding still is necessary.
3. Dry grinding processes do generate more internal heat than wet grinding.
With higher and higher standards required by paint and coating industries, fine grinding/particle
size reduction has become one of the most important factors for success. Over the years Attritors
have proven to be an excellent and reliable means to achieve these milling tasks.
9
General Rules of Thumb of Size Reduction
1. A specific type of machine (with fixed media, fixed operating conditions, and/or fixed
equipment parameters) is most efficient in grinding a certain type of material with a certain
range of feed size.
2. Size reduction over a large size reduction ration, for example (feed size/product size)>10.0, is
most efficiently accomplished by using a series of grinding stages, such as grinding machines in
series, the same machine used several times in sequence, or machines combined with
classification steps.
3. There is no single machine type that will grind large particles to a very fine material
efficiently by repeating or prolonging the process in the same machine.
4. To avoid over grinding of material that is already smaller than some desired size, this fine
material should be removed as soon as possible by classification. This process can increase
grinding throughput.
5. Uniform feed size can improve grinding efficiency a great deal.
6. Production is increased and the specific energy reduced only when a grinding circuit is
operated so that the size distribution is the most steep on a Schuhman plot (i.e. the most narrow
size range).